Additive manufacturing in polypropylene: a fully operative reality
We were the first Spanish firm and one of the few European companies that committed to this technology as soon as HP put it on the market, a bit more than one year ago. The learning curve has been tough. However, today our 3D division is fully operative: increasingly more companies are reaping the advantages of moving from an idea to the real physical part in record time.
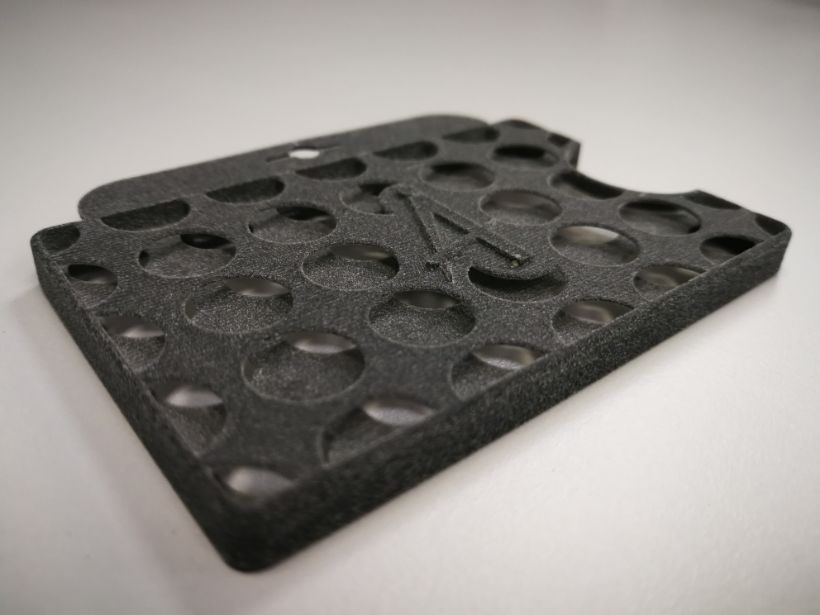
Our division dedicated to additive manufacturing has only been operative for a few months, but it has been working non-stop. Commissions are now common for the production of pre-series, prototypes and projects aimed at validating changes in part designs.
Accelerating innovation
Until now, demand has been led by the most competitive industry and by several research organisations. The fact is that for this type of professional equipment, 3D printing with polypropylene means having real and fast responses. ‘Thanks to this technology’ – commented Amparo Vázquez, our RD Manager – ‘solutions can be proposed, modifications explored and changes validated having the parts in our hands and going through the entire cycle quickly. What we are offering other industries is the ability to accelerate their innovation processes to become more competitive.’
Beyond prototypes
However, the possibilities of additive technology go much beyond validating parts and prototypes. That is because, at the end of the day, we are working with polypropylene, a polymer that has the same characteristics as injection with this HP Multi Jet Fusion technology: it is resistant to chemicals, with low water absorption and can provide functional parts.
That’s why the demand in our incipient 3D division is starting to expand both inside and outside of the automotive sector, with orders for tools, spare parts and custom parts.
‘Working with additive manufacturing has huge advantages,’ commented the innovation manager again, who pointed out three particular features:
- We can undertake morphologies that would be impossible with injection.
- We obtain lighter parts than traditional ones.
- We can create complex parts that would otherwise require assembly.
Full service
But, how do we approach projects that employ additive manufacturing? For our colleague Mónica Alegre, the Sales Manager, the answer is easy: ‘just like we handle projects for injection, by applying a full supply philosophy’. And she explained: ‘We provide our know-how to the entire project and make it available to clients from the preliminary study to the final part execution. It also has many other advantages, such as acquiring complete material beds for lowering prices, attending to urgent orders and providing personalised services.’ Simple, fast and, above all, highly efficient.